ISO OEM precision stainless steel spindles
Recently, the small robotic arm of the Suiwentian experimental cabin has successfully completed a series of on-orbit function and performance tests. All indicators have performed well and achieved the expected results. Today, I will show you the whole process of the on-orbit test of the small robotic arm in the Wentian experimental cabin. ISO OEM precision stainless steel spindles
What is a small robotic arm? As one of the “star” components of the space station, the small robotic arm is more compact than the large robotic arm equipped in the core module. It adopts a 7-degree-of-freedom symmetrical configuration with an end effector at each end; its arm is nearly 6 meters long. , the effective operating space is about 5 meters, and the maximum load is 3 tons; it can be used alone, or it can form a combined robotic arm with a large robotic arm; it supports astronauts’ out-of-vehicle activities, extra-vehicular status inspection, extra-vehicular cargo transfer and installation, and extra-vehicular maintenance. 6 application tasks including maintenance, load care and maintenance of optical facilities.
The small robotic arm ascended with the cabin for the first time and confirmed its functions and performance on-orbit. What are the test contents? Let’s find out together!
- Unlocking pyrotechnics
For the on-orbit test of the small robotic arm, the first thing to do is to unlock the pyrotechnics. After unlocking, the small robotic arm can be powered on to start various tests. Aerospace pyrotechnic device is a general term for disposable components and devices that ignite gunpowder, detonate explosives or perform mechanical work. ISO OEM precision stainless steel spindles
- Product self-inspection
After the small manipulator is unlocked, the on-orbit test of the small manipulator is gradually launched. The researchers first checked various products of the robotic arm, and the inspection contents mainly included controller status confirmation, joint inspection, end inspection, etc.
Three, single joint expansion
Single-joint deployment is to test each joint of the small robotic arm to confirm that the joints can be deployed normally. Completing various tasks such as fine operations and inspections in space requires a small robotic arm to have enough coverage. To this end, it is necessary to detect whether the single joint on the small robotic arm can be deployed normally. This is like the human joints, the joints can move freely, and the human can walk smoothly. ISO OEM precision stainless steel spindles
- Confirmation of crawling action
After the small robotic arm is deployed, it will confirm the crawling action on the bulkhead, which is an important basis for the robotic arm to perform extravehicular operations. The crawling of the robotic arm seems easy, but in fact there are many technical difficulties. The adapter docked during the crawling process of the robotic arm is exposed to the effect of the space environment for a long time, and will face the risk of aging and degradation. To this end, the researchers will design an automatic closing device to protect the adaptor docked with the robotic arm on the bulkhead, but at the same time, it will also increase the difficulty of the robotic arm crawling, so it is necessary to confirm that the closing device can operate normally before performing the crawling task.
Five, off the base
After the end of the small manipulator is docked with the adapter on the bulkhead, the other end of the small manipulator needs to be detached from the base, which is the “first step” for the complete small manipulator. Just as walking requires one step at a time, when the second end of the small robotic arm is detached from the base, the small robotic arm can truly “walk” the bulkhead. Whether the small robotic arm can be successfully detached from the base determines its ability to carry out subsequent tasks.
- Solar wing, exit hatch inspection and load target calibration
During the crawling process of the small robot arm, it will pass through 4 small robot arm adapters on the bulkhead. Each adapter is like the “footprint” of the small robot arm. After the small robot arm passes through all the “footprints”, each adapter can be guaranteed. All points are tested and verified. During this process, the small robotic arm will perform the solar wing, exit hatch inspection and load target calibration at the same time. After everything is confirmed, the small robotic arm will return to its original position to form a long-term storage configuration. ISO OEM precision stainless steel spindles
- Joint testing
After the ground researchers test and confirm the small robotic arm, they will carry out a “triple-party joint test” of the astronaut, the small robotic arm, and the small robotic arm console. The astronaut will conduct an operation test on the small robotic arm on the console panel. This is the first time the Shenzhou 14 crew has controlled and operated the small robotic arm.
It can be said that the space station is equipped with two large and small robotic arms, which realize the practical function of 1+1>2 and meet the needs of the space station mission. ISO OEM precision stainless steel spindles.
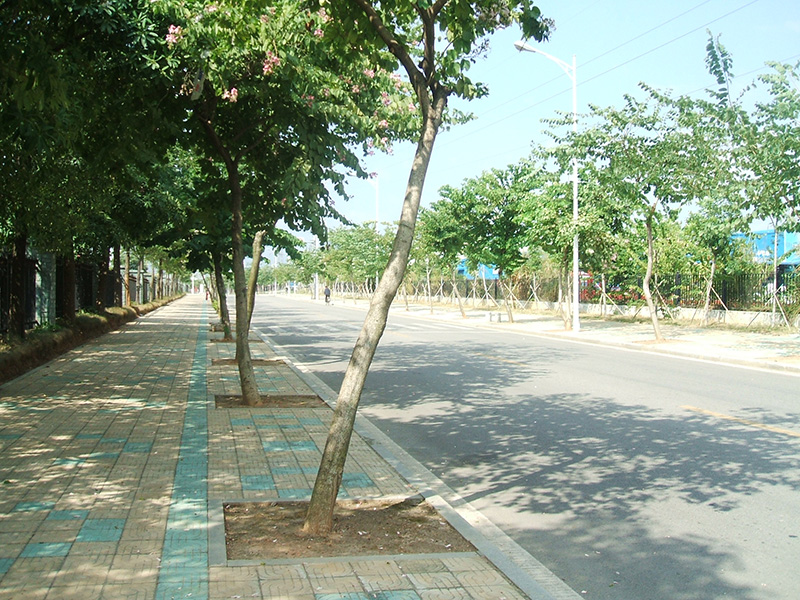
CNC Machining Service & CNC Machining partsCNC Machining Experts serving Global Industries. Deliver perfect parts, on time, at affordable prices. Armed with the industry-leading technology and techniques. All samples are free!China’s largest manufacturing companies. Precise component manufacture ltd. Rapid prototype machining, rapid prototype parts.