RoHS Approved Manufacturer of CNC machining process
In addition to price, the selection factors of refractory materials should also consider the following factors: longer service life; better thermal insulation effect; simpler masonry method and faster masonry speed; fast maintenance speed and so on. RoHS Approved Manufacturer of CNC machining process
Unshaped refractories, also known as bulk refractories, are composed of bulk particles and fine powders, and do not need to be fired or formed before use. It can flexibly change the composition properties and processes of materials according to needs, such as the composition and particle size of refractory materials; the type and amount of binders; additives (such as plasticizers, hardeners, retarders, water reducers) etc.) selection and adjustment and the diversification of construction methods (casting, ramming, spraying, projection, plastic construction, etc.) make the shape of refractory bricks develop a big step towards large-scale, special-shaped and integrated structures , known as the second generation of refractories.
Unshaped refractory material is one of the important basic materials in the application of high temperature furnace industrial refractory lining technology. Refractory castable is an important type of unshaped refractory material. Its important characteristics are that the supply cycle is short, and it is not limited by the shape of the equipment. It is not pre-calcined. Ready-to-use refractory. Refractory castables can be used to make seamless linings, also known as integral refractories. Unshaped refractories such as high-alumina castables, high-alumina low-cement castables, steel fiber wear-resistant castables, and corundum castables have been widely used in the lining design of cement kilns. Refractory layer of thermal equipment. RoHS Approved Manufacturer of CNC machining process
- Classification of unshaped refractories
1.1 Grout
A material with good fluidity after adding water and stirring, also known as pouring material. After molding, it needs to be properly maintained to make it coagulate and harden, and it can be used after baking according to a certain system. The grouting material uses aluminum silicate clinker, corundum material or alkaline refractory clinker as the aggregate; the lightweight grouting material uses expanded perlite, vermiculite, ceramsite and alumina hollow spheres as the aggregate. Calcium aluminate cement, water glass, ethyl silicate, polyaluminum chloride, clay or phosphate are used as binders. The admixture depends on the usage, its role is to improve the construction performance and improve the physical and chemical properties.
The construction and molding methods of grouting include vibration method, pump injection method, pressure injection method, spray method, etc. The overall lining is made of grout, and it is often used in conjunction with metal or ceramic anchors. If it is reinforced with stainless steel fiber, its resistance to mechanical vibration and thermal shock can be improved. The grouting material is used as the lining of various heat treatment furnaces, ore roasting furnaces, catalytic cracking furnaces, reformers, etc., and also used as the lining of melting furnaces and high-temperature melt launders, such as lead-zinc melting furnaces, tin baths, salt baths Furnace, tapping or tapping trough, ladle, suction nozzle of molten steel vacuum circulation degassing device, etc. RoHS Approved Manufacturer of CNC machining process
1.2 Plastics
Plastic mud or mud. When the appropriate external force is applied, it is easy to deform without cracking; after the stress is removed, it will not deform anymore. Plastic materials include semi-silica, clay, high alumina, zircon, carbon, etc., as well as lightweight plastics. Plastics must be added with plasticizing materials, most of which are high plasticity clays, and plasticizers can also be used to improve the plasticity of this clay. Plasticizers include carboxymethyl cellulose, dextrin, lignosulfonate and the like. The binders used for plastics include plastic clay, phosphoric acid, aluminum dihydrogen phosphate, aluminum sulfate, and the like. Alumina plastics with phosphoric acid or phosphate binders will chemically react with alumina during storage to generate insoluble aluminum orthophosphate and harden the mud, so preservatives such as oxalic acid, citric acid, acetyl Acetone etc.
The construction method generally adopts the ramming method or the vibration method. When building an integral furnace lining with plastic, metal or ceramic anchors must be provided. Plastics can be used as the lining of thermal equipment such as soaking furnaces, heating furnaces, boilers, etc., and also used to wrap the water cooling pipes of heating furnaces. RoHS Approved Manufacturer of CNC machining process
1.3 Gunning material
A refractory mixture used for gunning or spraying with a jet machine. According to the gunning method, it can be divided into wet gunning (or mud gunning), semi-dry gunning and fire (flame) gunning. Wet gunning uses compressed air to spray mud containing 20-40% refractory powder, which can achieve high fog dispersion, high adhesion rate, and can carry out relatively uniform thin-layer gunning. The semi-dry gunning is to add water to the nozzle to wet the refractory powder sprayed by compressed air. The amount of water added is 11-14%, and the adhesion rate is low, and thicker layer gunning can be carried out. Fire gunning belongs to dry gunning. The gunning material is sent to the flame of the fuel-oxygen spray gun, and the gunning material is partially melted in the nozzle flame and attached to the brick lining.
The gunning material is made of aluminum-silicon, aluminum-silicon-zirconium, magnesium, magnesium-calcium, magnesium-chromium, etc. The binders used are sodium silicate, phosphate, polyphosphate, asphalt, resin and the like. In order to improve the adhesion rate, additives such as clay, bentonite, and lime are added. In order to ensure that the gunning material can achieve good sintering, a sintering aid is also added, such as serpentine, pure olivine, lime, refractory clay, iron oxide, etc.
1.4 Refractory Coatings
The material applied to the lining of refractory bricks. Depending on the requirements of use and construction methods, refractory coatings are formulated into paste-like and mud-like forms. The binder used varies depending on the material, such as alkaline coatings phosphate, polyphosphate, magnesium sulfate for the preparation of continuous casting tundish; clay, aluminum dihydrogen phosphate, aluminum chromium phosphate, water glass, etc. for the preparation of high-alumina coatings . In order to improve the spreadability of coatings, additives such as plasticizers are generally added. The coating is mainly used as a protective coating for the lining of various thermal equipment, or for repairing local damage to the lining of bricks. RoHS Approved Manufacturer of CNC machining process
1.5 Ramming material
A bulk refractory material with very low or no plasticity. The materials are siliceous, clay, high alumina, corundum, zircon, silicon carbide, carbon, magnesia, etc. According to the material of the ramming material and the conditions of use, inorganic binders or organic binders similar to the pouring materials can be used, such as water-soluble dextrin, carboxymethyl cellulose, lignin, sulfonate, polyvinyl alcohol; water-resistant and Thermoplastic paraffin, asphalt, tar, phenolic resin, random polypropylene, etc.
The ramming material is constructed by forced ramming, with low porosity and high density. Therefore, among the unshaped refractories, the ramming material is especially suitable for the lining of melting furnaces and various containers containing high-temperature molten metal. Such as open hearth and electric furnace hearths, various induction furnace linings, blast furnace tapping ditch, ladle and so on.
1.6 Projection material
A semi-dry, lined mud that is projected with a projector. Mainly used to build the lining of the overall steel ladle. The materials are siliceous, alabaster, clay, high alumina and zircon. The most used are high-silica and high-alumina projection materials.
- Application of unshaped refractory materials
2.1 Characteristics of castable prefabricated blocks
The castable prefabricated block only needs to be heat treated at a lower temperature, it is a low carbon and green refractory material, and it is a unique technology in the refractory lining technology. It can improve the performance of the refractory lining, reduce the consumption of refractory materials, and has stable quality and reliable performance. We know that the purpose of adding steel fibers to the castable is to improve the mechanical properties of the castable, inhibit the occurrence of cracks or limit the propagation of cracks when they are formed. The figure below is a diagram of the steel fiber castable. The steel fiber castable prefabricated block is made by a special process. According to the process position and needs, it is made into a certain shape, and after demolding, heat treatment is carried out according to its working conditions. RoHS Approved Manufacturer of CNC machining process
2.2 Application of Unshaped Refractories in Blast Furnace
Blast furnace is an important equipment for iron making. Small blast furnaces used to be hoisted and built with high alumina cement and high alumina phosphate refractory castable prefabricated blocks. Now resin-bonded aluminum carbon unburned bricks are commonly used for masonry. Large blast furnace water walls The SiC castable is used for ramming, and the furnace bottom cushion and the surrounding brick joints are made of refractory castable and silicon nitride filler. A development trend of the refractory material for the furnace wall is to use castable. Japan Steel Pipe Company Fukuyama Plant No. 2 The blast furnace uses a high-density castable of Al2O350% and SiO245% on the top of the furnace body. After 6 years of use, it is found that spalling rarely occurs.
At present, the unshaped refractories used for blast furnace tapping trenches at home and abroad are mainly Al2-O3-SiC-C (ASC for short), in addition to mullite-SiC-C, Al2O3-C, magnesium-aluminum spinel Corundum-SiC castables are mainly used in my country. In Japan, most blast furnace taps use ASC castables and repair gunning materials, and some small blast furnace taps use bauxite or synthetic mullite- SiC-C quality ramming material. ASC quality ramming material is generally used in the blast furnace tapping trenches in Germany and France. France has developed a self-flowing castable, which improves the working life of the main tapping trench. RoHS Approved Manufacturer of CNC machining process
2.3 Application of Unshaped Refractories on Ladle
The increase of the tapping temperature and the prolongation of the residence time of the molten steel in the ladle have caused great changes in the refractory materials used in the ladle. The ladle used to be dominated by shaped refractories, but is now replaced by amorphous refractories. It can not only save labor, but also realize the automatic construction and drying of the factory, and improve the overall economy. When the side wall of the ladle is indefinite, the maintenance operation time can be saved by 40%. When the lining of the ladle is all indefinite, the labor-saving effect is 70%. %. Because Al2O3-spinel castable has the advantages of good corrosion resistance, small structural spalling, long service life and can improve the quality of steel, it has become the main role of the current ladle refractory. However, its use is affected by temperature. Due to the limitation of the residence time of molten steel, the Al2O3-MgO castable developed by Kawasa-ki Company of Japan has improved material strength and slag penetration resistance, and its life is 20% higher than that of Al2O3-spinel castable. The magnesia refractory castables and the aluminum-magnesium carbon refractory castables have also been tried out, and initial results have been achieved.
2.4 Application of Unshaped Refractories in Nonferrous Metallurgy
(reverberatory furnace)
Aluminum reverberatory furnace is a large consumer of refractory materials in aluminum plants. The refractory materials for hearth have changed from brickwork to integral structure. The refractory materials in contact with the metal on the hot surface of the hearth are usually acid-bonded plastics, phosphate-bonded bricks and Low cement castable, the composition of the hot surface refractory of the lower side wall is usually the same as that of the hearth, and the thermal insulation material can be made of light thermal insulation castable, thermal insulation clay brick or ceramic fiber, etc.; High-quality refractories such as castables; furnace doors are usually cast with dense castables or light castables, or a mixture of the two. RoHS Approved Manufacturer of CNC machining process
In electrolytic aluminum smelting, amorphous refractory materials are mainly used in aluminum barrels. The refractory material for the aluminum bucket is required to be able to resist the erosion of aluminum water, to withstand the effect of rapid cooling and rapid heating, and to have good thermal insulation performance. The non-working lining of the aluminum bucket generally adopts lightweight castables or lightweight high-alumina bricks. The molten aluminum needs to be placed for a long time, and heat-insulating castables are usually used to prevent the molten aluminum from solidifying during transportation. Now, in order to reduce the self-weight of the tank and enhance the thermal insulation effect, alumina hollow ball refractory castables are used for non-working linings. The working lining is generally made of high-alumina bricks with low SiO2 content, and some tanks are now made of corundum refractory casting.
In the copper smelting industry, because CuO is very corrosive as a component of slag, basic refractory materials are widely used in rough smelting furnaces. Magnesia-chrome bricks or MgO-based alkaline ramming materials, especially for repairing and repairing furnaces. Due to the decrease in slag amount and temperature in the refining part, castables, plastics, spray coatings and high-alumina bricks can be used. Aluminum acid refractory material. RoHS Approved Manufacturer of CNC machining process.
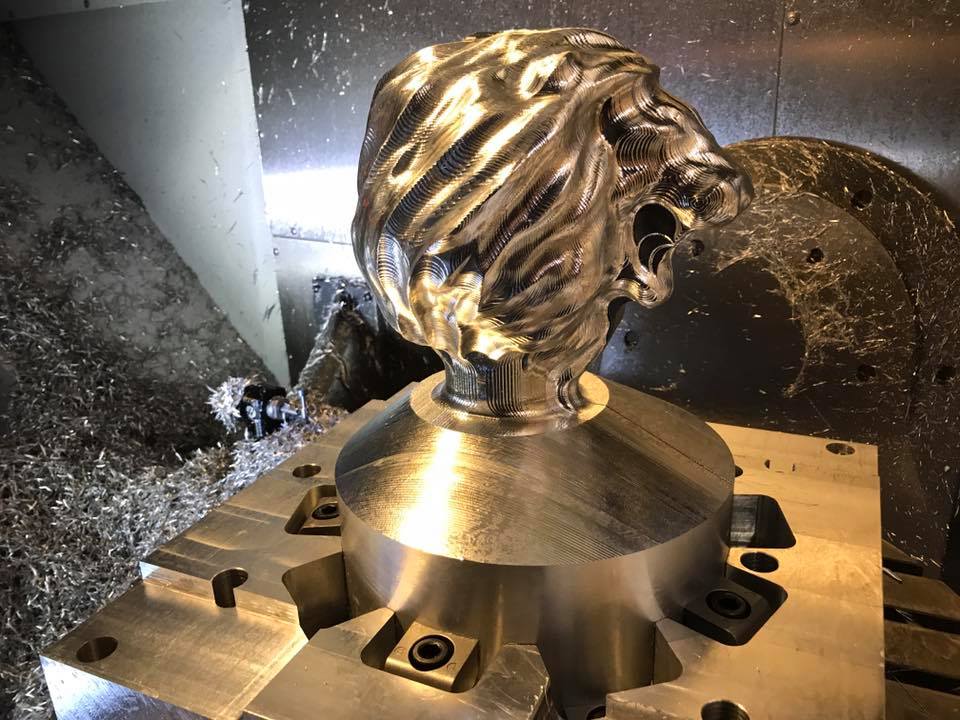