Three basic principles of non-principle. plastic machining
First, do not accept unqualified products
Not accepting unqualified products means that before the production and processing, the employees shall check the passing quality of the products they have passed, and if they find a problem, they have the right to refuse acceptance and feedback to the previous process. The former process personnel need to immediately stop the processing, trace the reasons, and take measures so that the quality problems can be found and corrected in time, and the waste caused by continued processing of non-conforming products can be avoided. plastic machining
Second, do not produce defective products
The failure to manufacture non-conforming products means that after accepting qualified products from the front line, the company strictly enforces the operation specifications at the time of processing in this position to ensure the quality of the products processed. Pre-operational inspections, confirmations, and other preparations are done well; the process status in the operation is followed with wild birds, to avoid or early detection of abnormalities, and to reduce the probability of unqualified products. Being fully prepared and confirmed during the process is the key to not creating a nonconformity. Only by not producing bad products can make it possible to not flow out and accept bad products.
Third, do not flow out of defective products
The non-conforming non-conforming product means that the employee completes the processing of the process and needs to check and confirm the product quality. Once a defective product is found, it must be shut down in time, the defective product must be cut off in the process, and the defective product must be disposed of in this process and preventive measures must be taken. . This process should ensure that the pass is a qualified product and will be rejected by the next process or “customer”. plastic machining
Three points of non-principle implementation
First, who makes who is responsible
Once the product design and development are completed and the process parameters are clearly defined, the product quality fluctuation is a problem in the manufacturing process. Everyone’s quality responsibility begins with accepting qualified products from the previous process. It is the employee’s biggest task to standardize operations and ensure that the product quality of the current process meets the requirements. Once unfavorable information is found in this process or after receiving feedback from subsequent processes, employees must immediately stop production, investigate the cause, and take measures to be responsible for the quality of the product. plastic machining
Second, who made who checked
The producer of the product is also the inspector of the product. Inspection of the product is only one part of the production process. By checking and confirming that the production is qualified, it can be ensured that the qualified product will flow into the next process. Through its own inspection, the operator can understand the status of the processed products in this process more clearly, which will help the employees to continuously improve the processing level and improve the product quality. plastic machining
Third, the standardization of operations
Starting from the design, development and setting of process parameters, the product must be standardized and standardized in all operational procedures and operation details, and be continuously improved. Every employee must also strictly implement standardized operations. Standardization is the best method of operation for this process, and it is the only way to ensure the consistency of product quality. Otherwise, there is no root cause for the failure to manufacture a lot of defective products. At this time, “three non-principles” can only create confusion, not quality.
Fourth, all check
All products, all processes in any form must be implemented by the operator to perform all inspections. plastic machining
V. In-process inspection
Quality is produced by the operator. If another inspector is arranged to inspect or repair the product outside the process, it will cause waste, and it will not improve the sense of responsibility of the operator. It will also disregard the operator’s disregard for the quality of his products.
Sixth, bad stop production
Once a defective product is found within the process, the operator has the right and the responsibility to stop the production, and take timely investigation of countermeasure activities. plastic machining
Seventh, the current processing
In the production process, when a non-conforming product is produced, the operator must change from the production state to the investigation and processing state, immediately stop the operation and promptly confirm the on-site elements such as the person, machine, material, and law ring that produce the defective product. “The real culprit” and deal with it in time. plastic machining
Eight, poor exposure
Any defects that appear in the production process must have its own internal causes. Only by truly solving each of the causes of the defects, can we control the manufacturing of nonconforming products and achieve zero defects, so as to truly satisfy customers. Therefore, for the occurrence of defects, not only the operator must know, but also must let the management know that the quality assurance personnel know that the design and development personnel know that everyone will carefully analyze the countermeasures and improve the operating standards, not simply by the operation. Qualified products are reworked or scrapped; otherwise, the same problem will occur the next time. plastic machining
Nine, foolproof and mistake-proof
The quality of a product cannot be completely relied on by the responsibility of the operator to ensure that any person will have emotions, be inert, be fortunate, and be subject to some unexpected factors, which will fluctuate the quality of the product. Therefore, the use of fool-proof and error-proof devices must be designed as scientifically and reasonably as possible to prevent inattention. At the same time, in the on-site management, careful management of details, as much as possible to do work in the front, comprehensive planning, adequate preparation, prevention in advance, reduce the variety of changes, the quality of control in the required range. plastic machining
Ten, management support
Operators take responsibility for the quality of the product, but the product is defective. Management should take more responsibility because the role of the site manager is to help the staff solve the problem. When an employee finds a problem and reports it, he or she should be present at the scene as a site manager and investigate and resolve the issue together. If the unscrupulous goods merely shirk their responsibility to the operators, not only can they completely eliminate the production of non-conforming products, but they can also cause conflicts between management and employees. Therefore, if you want to guide employees, prevent problems in advance, analyze problems together with employees, and investigate and solve problems, you must provide the necessary resources and facilities for employees, and must help employees relieve their worries about life and work. In short, the manager can only be a strong backing for employees, and “three non-principles” can truly be implemented in production. plastic machining
CNC Machining Service & CNC Machining parts
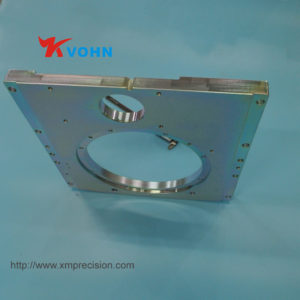
precision machining company