A. Outer diameter taper of cylindrical workpiece after processing. China Precision CNC Machining Services manufacturer
cause:
1, headstock spindle center line, the non-parallel degree of the guide rail movement guide rail.
2. The inclination of bed rails is poor or deformed after assembly.
3. The bed surface of the bed is heavily worn. The non-straightness of the slide plate in the horizontal plane and the inclination of the slide plate have been exceeded.
4. Because the centerline of the spindle taper hole and the centerline of the tailstock cone sleeve are not on the same line.
5, the impact of the tool, the blade is not wear.
6. The temperature rise of the bedside box is too high, causing thermal distortion of the machine tool: the spindle in the headstock, bearing friction clutch, gears and other transmission parts, due to the movement and frictional heat, its heat is absorbed by the lubricating oil, becoming a larger With the secondary heat source, heat is transmitted from the bottom of the headstock to the bed and headboard, which increases the temperature of the bed joint and causes the expansion to cause the machine tool to undergo thermal deformation. China Precision CNC Machining Services manufacturer
Solution:
1. Correct the installation position of the centerline of the headstock spindle so that the workpiece is within the allowable error range.
2. Use the adjusting horn to recalibrate the inclination of the bed rails.
3, when the slide is not straight in the horizontal plane and the inclination of the carriage is small when the deviation is small, there is no large area scratch on the guide rail surface, and the guide rail can be used to repair. If the out-of-tolerance is large, the guide rails or the guide rails should be polished.
4. Adjust the screws on both sides of the tailstock to eliminate the taper.
5. Trim the tool and correctly select the spindle speed and feedrate.
6, to the cold state processing accuracy of the workpiece, but after hours of operation of the workpiece is only out of tolerance, that should be properly adjusted the spindle front bearing oil supply, replace the appropriate lubricant, check the oil pump inlet is blocked. China Precision CNC Machining Services manufacturer
Second, the workpiece after processing oval and ellipsoidal
cause:
1, spindle bearing clearance is too large (because of more particles in the mechanical wear of lubricants, the critical friction when the bearing under heavy load, the lack of oil supply or block, etc. will cause the bearing to cause serious wear).
2. The ellipticity of the spindle journal is too large.
3, spindle bearing wear, or the spindle last stage gear accuracy is poor, there is vibration when rotating.
4. The outer diameter of the bearing sleeve of the main shaft is elliptical or the shaft hole of the headstock box is elliptical, or the gap between the two is too large.
5, the tip of the machine tool tip, or the workpiece thimble hole is not round. China Precision CNC Machining Services manufacturer
Solution:
1. Adjust the clearance of the spindle bearing; if the lathe is often working at high speed, the adjustment gap should be slightly larger, and if it is often working at low speed, the clearance should be smaller. If the spindle clearance is adjusted at a low speed, the pivoting phenomenon may occur at high speeds. Therefore, it should be adjusted according to the daily operating specification speed range of the lathe, and the general clearance should be between 0.02~0.04mm.
2. Grind the shaft journal of the spindle to meet the roundness requirements.
3. Scrape the bearing, grind the journal, replace the rolling bearing or the last stage gear.
4. If the out-of-roundness taper of the shaft hole is poor, it should be scraped first, then straightened, and then repaired with “partial nickel plating”; if it is a sliding bearing, a new bearing sleeve must be replaced.
5. Trim the thimble or workpiece thimble hole. China Precision CNC Machining Services manufacturer
Third, when the outer surface of the fine car, repeated at a certain length of the ripple
cause:
1. The longitudinal gears of the carriage box do not engage with the rack.
2. The bent holes of the polished rod or the polished rod, screw rod, and cutter rod are not on the same plane.
3. Damage to a transmission gear (or worm gear) in the carriage box, or incorrect kneading due to pitch fluctuations.
4. Bending of the shaft or damage of gears in the headstock and the feed box.
Solution:
1. If the distance between the corrugation is the same as the pitch of the rack, it can be considered that the corrugation is caused by the rack-gear. The meshing clearance should be adjusted, and the rack and pinion should mesh on the full width of the tooth surface.
2. In this case, only regular periodic ripples are repeated: If the polished rod is bent, the polished rod should be straightened out; the three holes must be kept coaxial and on the same plane during assembly; the slide must not be moved when moving.
3. Check and correct the transmission gear in the carriage box and replace it if it is damaged.
4, check the drive shaft and gear, straighten the drive shaft, replace the damaged gear. China Precision CNC Machining Services manufacturer
Fourth, the fine car outer circle, in the circumferential surface of the spindle axis line parallel or at an angle, repeated regular ripple
cause:
1. Gear teeth wear or kneading on the spindle.
2. The gap between spindle bearings is too large or too small.
3. The vibration of the machine tool is caused by reasons such as the outer diameter of the pulley on the headstock or the vibration of the belt slot. China Precision CNC Machining Services manufacturer
Solution:
1. When such ripple occurs, if the number of ripples (or the number of ripples) is the same as the number of teeth of the transmission gear on the main shaft, it can be determined that it is caused by the transmission gear on the main shaft. This situation generally occurs after the spindle bearing is adjusted and the meshing clearance of the gear pair is not suitable. The meshing clearance should be maintained at about 0.05 mm; when the meshing gap is too small, the grinding paste can be used to grind the gears and then completely disassembled and cleaned. When the meshing gap is large or the tooth wear is severe and the ripple cannot be eliminated, the main shaft gear must be replaced.
2, adjust the spindle bearing clearance. Axial runout of the rolling bearing is <0.005 mm.
3. Eliminate the eccentric swing of the pulley, adjust the clearance of its rolling bearing, and eliminate other vibration sources that cause the vibration of the machine tool.
5. When the fine car is round, there is a section of corrugated protrusions on the circumferential surface of the workpiece. China Precision CNC Machining Services manufacturer
cause:
1, bed rails in the fixed length position bump bumps and so on.
2. The surface of the rack protrudes or the joint between the racks is poor.
Solution:
1, repair scratches and other burrs.
2. Check and correct the joints of the two racks and rest the protruding surface of the rack so that it has the same tooth thickness as other single tooth surfaces.
6. When the fine car is round, there is chaotic ripple on the circumferential surface. China Precision CNC Machining Services manufacturer
cause:
1. The raceway wear of the main shaft rolling bearing.
2. The axial clearance of the main shaft is too large.
3, the use of tailstock to support the workpiece cutting, the top set of instability.
4. When the workpiece is clamped by the chuck, the internal thread of the chuck flange hole and the centering journal thread of the front end of the spindle are loosely fit, causing the workpiece to be unstable, or the shape of the claw becoming a flare hole, so that the workpiece is not clamped. stable.
5. The square tool holder is deformed due to the clamping tool, which causes poor contact between the ground and the surface of the upper knife holder base plate.
6. The clearance between the sliding surfaces of the upper and lower blade holders (including slide plates) is too large.
7. The three supports of the knife box and the carriage box bracket have different shafts, and the shaft rotates vigorously (blocking phenomenon). China Precision CNC Machining Services manufacturer
Solution:
1. Replace the main shaft of the rolling bearing.
2. Adjust the backlash of the main shaft rear thrust ball bearing.
3, check the tailstock top sleeve and shaft hole and clamping device, such as loss of function, you can first repair the shaft hole, and then according to the actual size of the bearing after repair, single tailstock top sleeve.
4, change the workpiece clamping method, with tailstock support for cutting. If the random pattern disappears, it can be determined that it is due to the wear of the chuck flange. In this case, a new chuck flange can be configured according to the centering journal and the front end thread of the spindle. If the chuck is a horn hole, copper pads can be added to solve the problem.
5. Scrape and trim the joint surface of the square tool holder so that it can reach a uniform and full contact.
6. Adjust the plug iron pressure plate of all guide rails to make it evenly fit and shake smoothly and lightly.
7. Check the supports and remove them if necessary.
Seventh, when the fine car is round, there is a vibration mark on the circumferential surface of each rotation of the main shaft. China Precision CNC Machining Services manufacturer
cause:
1. Some of the rollers of the main shaft rolling bearing wear badly.
2. The shaft diameter of the transmission gear is excessively large.
Solution:
1, replace the bearing.
2. Eliminate the pitch fluctuation of the main shaft gear, and replace the gear pair when serious.
Eight, after finishing the car, the workpiece end convex
cause:
1. The non-parallelism of the centerline of the headstock spindle of the headboard movement is very poor.
2, the upper and lower guide rails are not vertical deviation. China Precision CNC Machining Services manufacturer
Solution:
1. Correct the position of the spindle centerline of the headstock. Under the premise of ensuring the correct cone of the workpiece, the centerline of the spindle is forward biased, that is, it is biased toward the toolholder.
2. Scrape the guide rail surface of the slide plate, and bias the outer end of the upper rail of the slide plate toward the headstock.
Nine, when the finish car face, no parallelism occurs
cause:
1. The surface of the upper rail of the slide plate is not straight.
2, in the dragging plate screw and nuts do not mind.
Solution:
1, scraping and straightening the upper rail surface.
2, rest screw, nut, ensure concentric. China Precision CNC Machining Services manufacturer
Tenth, the end of the fine car after the shock
cause:
1. The axial clearance of the main shaft is too large or the axial turbulence is excessive.
Solution:
1. Adjust the axial clearance and turbulence of the spindle to ensure that the tolerance is within 0.02mm.
Eleven, when finishing the large end workpiece, the ripples are repeated at regular intervals in the diameter direction. China Precision CNC Machining Services manufacturer
cause:
1. When the slide rails wear on the slide, the gaps and other unstable phenomena occur when the carriage is moved down.
2, horizontal screw bending.
3, horizontal screw and nut due to wear and clearance is too large.
Solution:
1, scraping with guide rails and plug iron, so that the knife holder is stable when the lower seat moves.
2, straighten the horizontal screw.
3. Adjust the gap between the screw and the nut. After loosening the screw on the left side nut, pull the neodymium iron with the middle screw and adjust it to the proper clearance. Then tighten the left nut. China Precision CNC Machining Services manufacturer
Twelve, uneven thread pitch and chaos when turning threads
cause:
1. The spindle of the machine tool is worn and bent. The wear of the opening and closing nut is different from that of the screw shaft and the meshing is poor. The clearance is too large. It is caused by the instability of the opening and closing nut when the dovetail guide rail is worn.
2. The clearance of the drive chain from the main shaft through the hanging wheel is too large.
3, the axial clearance of the screw is too large.
4. The male and female handles are attached to the wrong position, the position of the fork is not correct, or the hanging wheel is hanging on the wheel carrier. China Precision CNC Machining Services manufacturer
Solution:
1. Straighten the screw rod, adjust the gap between the screw rod and the opening and closing nut pair, repair and scrape the dovetail guide rail, and ensure that the opening and closing nut is stable when closed.
2. Check the meshing clearance of each transmission element. All the adjustments are adjustable, such as hanging wheels, etc.
3, adjust the screw axial clearance and turbulence.
4, check the handle, the fork, the hanging wheel is correct, change the wrong. China Precision CNC Machining Services manufacturer
XIII. Ripple on the surface of the workpiece after finishing the car
cause:
1, due to the wear of the machine tool, the slide plate tilts and sinks, so that the screw bending and the opening and closing nut are in poor meshing and meshing.
2. The support hole of the bracket is worn out, making the rotation centerline of the screw unstable.
3, the axial clearance of the screw is too large.
4. The hanging axle of the knife box is bent.
5. There is a gap between the carriage and the carriage in the square cutter head.
6. The contact surface between the square knife holder and the bottom plate of the knife holder is in poor contact. China Precision CNC Machining Services manufacturer
Solution:
1. The slide plate is repaired with an additional compensating ring, that is, a layer of guide plate is bonded with adhesive on the lower guide surface of the slide plate so as to compensate the amount and inclination of the slide box sinking due to wear of the guide rail.
2. Bracket holes in the bracket support hole.
3, adjust the axial clearance of the screw. Should be guaranteed within ≤ 0.01 mm.
4, replace the curved shaft.
5, adjust the rail surface clearance and plug iron, pressure plate and so on. Each sliding surface is checked with a 0.03 mm feeler gauge and the insertion depth should be ≤ 20 mm.
6. Repair the base surface of the knife holder and wipe the contact points of the four corners.
After the compression handle on the square tool holder is pressed tightly, the handle of the knife holder will not turn. China Precision CNC Machining Services manufacturer
cause:
1. The bottom of the square cutter is not flat.
2. The contact surface between square tool holder and small tool holder base plate is poor.
3. After the tool holder is pressed tightly, the square tool holder is deformed.
Solution:
1. Use a spatula to scrape the bottom of the square knife holder and keep it in good contact.
2. Scrape the contact surface with a spatula to ensure good contact between the knife holder and the small knife holder.
3, check the amount of deformation, repair the deformation site. China Precision CNC Machining Services manufacturer
CNC Machining Service & CNC Machining parts
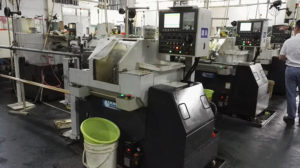
Experienced aluminum machining services China Manufacturer
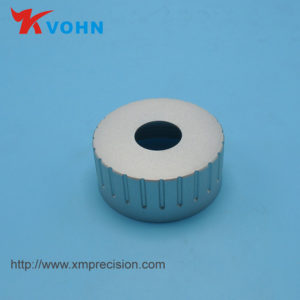
milling components
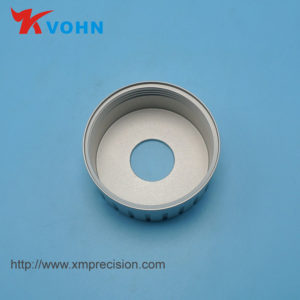
ceramic machining services