Professional high precision cast iron coupling
The advantages of drilling and turning tools in CNC machining are analyzed, and a set of application skills are summarized on how to use this tool well, and the cutting parameters for drilling and turning tools are given for different processing materials. Compared with conventional machining methods, the application of drilling and turning tools significantly improves the machining efficiency. Professional high precision cast iron coupling
1 Preface
Drilling tool (see Figure 1) is a high-efficiency, compound and multi-purpose tool, but in CNC machining, improper use will cause many problems and cannot achieve the effect of use. In machining, there is a difficult problem that everyone cannot avoid: the more complex the workpiece shape, the more machining tools, and the higher the tool change frequency, resulting in increased workpiece processing time. This problem has become a bottleneck that hinders the improvement of production efficiency in machining.
With the rapid development of CNC tool technology, many high-speed and high-efficiency multi-function tools have emerged. 1]. The drilling and turning tool has changed the single function of the previous tool. One tool can simultaneously complete four high-precision and high-efficiency processing methods of face turning, drilling, internal hole turning and external turning, which greatly reduces the selection of tools during processing. The complexity of tool change and programming becomes a “multiplier” for efficient production. Professional high precision cast iron coupling
In order to make the multi-functional tool such as drilling and turning tools widely popularized and applied in CNC machining, and maximize the technical advantages of drilling and turning tools and CNC machine tools, the author aims at the problems that often occur in the practical application of drilling and turning tools in CNC machine tools. Summarized a set of general drilling and turning tools using skills, which significantly improved the processing efficiency.
2 Advantages of drilling and turning tools in CNC machining
1) The drilling and turning tool can simultaneously complete four high-precision and high-efficiency processing methods of face turning, drilling, boring and external turning. One tool can realize the functions of four tools, as shown in Figure 2.
a) Face turning b) External turning
c) Drilling d) Internal turning
2) When drilling a flat-bottomed hole, one tool can complete the tasks that require three tools: center drill, drill bit and flat-bottom drill in ordinary processing, and can ensure that the bottom surface is 90º vertical to the hole wall, and no additional processing is required. . Professional high precision cast iron coupling
3) The drilling and turning tool can realize the drilling and turning of multi-step holes, as well as boring, chamfering and eccentric drilling.
4) The drilling and turning tool can process holes with an accuracy of ±0.05um and a surface roughness value of Ra=1.6μm, and can achieve high feed, high speed and high efficiency cutting.
5) When drilling, the chips are mostly short chips. The internal cooling function of the tool itself can form a high-pressure cooling water flow for safe chip removal. It is not necessary to clean the chips on the tool, which is conducive to the continuity of product processing and shortens the processing time.
6) Under the standard length-diameter ratio machining conditions, there is no need to remove chips when drilling holes with a drill-turning tool. Professional high precision cast iron coupling
7) The drill-turning tool is an indexable single-edged tool. After the blade is worn, it does not need to be sharpened. The replacement is convenient and the cost is low.
8) The surface roughness value of the hole processed by the drilling and turning tool is low, generally reaching Ra=3.2μm, and the tolerance range is small, which can save part of the work of the boring tool.
9) After the cutting parameters of the drilling and turning tool are reduced by 30%, intermittent cutting can be realized, such as machining intersecting holes, intersecting holes and intersecting perforations.
10) The use of drilling and turning tool technology can not only reduce drilling and turning tools, but also because the drilling and turning tool uses a single-edged carbide insert on the head, its cutting life is 15 times that of ordinary drill bits. There are 4 cutting edges. When the blade is worn, the cutting edge can be replaced at any time for re-cutting without re-calibrating the tool, which saves a lot of time for grinding the cutting edge and changing the tool, and can increase the production efficiency by an average of 6 to 7 times. Professional high precision cast iron coupling
3 Problems of drilling and turning tools in CNC machining
1) The blade is damaged too quickly, and the tool is easily broken, which increases the processing cost.
2) There is a harsh noise during processing, and the cutting state is abnormal.
3) The jitter of the machine tool affects the machining accuracy of the machine tool.
4) Drilling and turning tools make holes on inclined surfaces, which is easy to cause tool damage.
4 Tips for using drilling and turning tools
1) The rigidity, rotational speed, tool and workpiece alignment of the machine tool are required to be high when the drilling and turning tool is used. Therefore, the drilling and turning tool is suitable for use on high-power, high-rigidity and high-speed CNC machine tools.
2) When using the drilling tool, the blade should be selected with good toughness and positive rake angle. Professional high precision cast iron coupling
3) When machining different materials, inserts with different geometries should be used. In general, when the feed rate is low, the tolerance is small, and the aspect ratio of the drill-turning tool is large, the inserts with smaller cutting force are used; otherwise, rough machining is performed. If the tolerance is large and the aspect ratio of the drill-turning tool is small, the grooved insert with a large cutting force is selected .
4) When using the drill-turn tool, be sure to consider the power of the machine tool spindle, the clamping stability of the drill-turn tool, the pressure and flow of the cutting fluid, and at the same time control the chip removal effect of the drill-turn tool, otherwise the hole will be affected to a great extent. surface roughness and dimensional accuracy.
5) When clamping the drill-turning tool, be sure to make the center of the drilling-turning tool coincide with the center of the workpiece, the error is less than 0.1mm, and it is perpendicular to the surface of the workpiece.
6) When adjusting the center height of the drill-turning tool, just rotate the drill-turning tool 180° each time (the bottom plane drilled by the drill-turning tool after adjusting the center will have a 0.1mm bulge). Professional high precision cast iron coupling
7) When using a drill-turning tool, appropriate cutting parameters should be selected according to different part materials.
8) During the trial cutting of the drill-turning tool, be sure not to reduce the feed rate or reduce the speed at will because of fear, so that the drill-turning tool blade is damaged or the cutter body is damaged.
9) Various problems will occur when using the drilling and turning tool for processing, and the various problems and corresponding solutions are shown in Table 2.
Table 2 Problems and solutions in drilling and turning tool processing
10) When using a drill-turning tool to process stepped holes, be sure to process large holes first, and then process small holes.
11) When using the drilling and turning tool, pay attention to the sufficient pressure of the cutting fluid (>1000kPa) to flush out the chips.
12) When drilling with a drill-turning tool, the workpiece rotation, tool rotation, and simultaneous rotation of the tool and the workpiece can be used, but when the tool moves in a linear feed mode, the most common method is to use the workpiece rotation method.
13) The cutting edge of the drill-turning tool blade needs to coincide with the center of the workpiece, otherwise the tool will be damaged too quickly, the tool will be easily broken, and the processing cost will increase.
14) When drilling through holes, remember to reduce the feed rate (by 50%) to avoid damage to the blade. Professional high precision cast iron coupling
5 Conclusion
The use of the above drilling and turning tools can effectively solve the problems that often occur when using drilling and turning tools for CNC turning and milling, and can effectively ensure the processing quality of parts. The machine tool can be perfectly combined to more effectively improve the use efficiency of the tool and the machine tool, so that the CNC machine tool can maximize its advantages of high efficiency and high precision. Professional high precision cast iron coupling
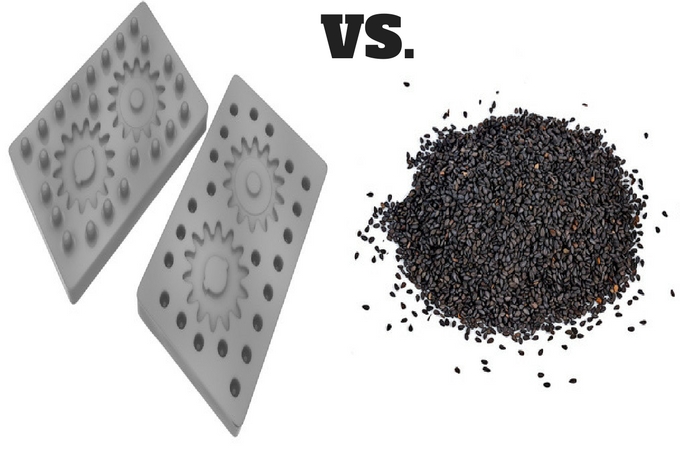